Overcoming Challenges with PCD Reamers: A Comprehensive Guide
Master the use of PCD reamer tools to boost manufacturing precision. Discover essential tips for overcoming common reaming challenges
Introduction to PCD Reaming
Polycrystalline Diamond (PCD) reamers stand at the forefront of precision manufacturing, offering unparalleled durability and finish quality. Used across industries, these tools are essential for achieving the high levels of accuracy required in today’s advanced manufacturing environments. This guide aims to illuminate the path for professionals navigating the complexities of PCD reaming, providing expert insights into overcoming common challenges, including hole diameter discrepancies and surface roughness issues frequently encountered during the reaming process.
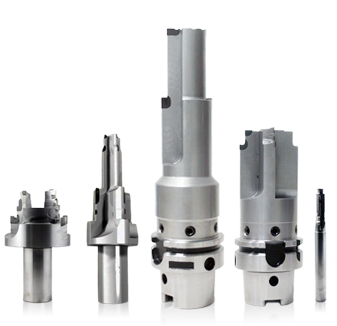
-What are PCD Reamers?
PCD reamers are cutting tools used in the machining process to enlarge or refine the diameter of previously drilled holes. Made from polycrystalline diamond, they are renowned for their hardness, wear resistance, and ability to produce a superior surface finish on machined parts.
-The Significance of Reamer Tool in Manufacturing
Reaming plays a pivotal role in manufacturing, serving as a critical step in ensuring the dimensional accuracy and finish of holes. Its importance cannot be overstated, as it directly impacts the assembly quality and functional performance of the final product.
The Most Common Problems Encountered During Reaming Using PCD Reamer tool
-Material Compatibility Issues
Identifying Compatible Materials
Not all materials are suited for reaming with PCD tools. Understanding material properties and their interaction with PCD is essential for achieving optimal results.
-Solutions for Material Compatibility
- Selecting the right tool geometry and reaming parameters
can mitigate compatibility issues, ensuring smooth operation and longevity of the tool.
-Tool Wear and Maintenance
- Recognizing Wear Patterns
Understanding wear patterns, such as increased hole diameter due to oversized PCD reamer dimensions or burrs on the reamer’s edge, is crucial for timely intervention, preventing damage to both the tool and the workpiece.
- Maintenance Best Practices
Regular inspection and maintenance, addressing issues like tool wear that leads to decreased hole size or poor surface finish, extend tool life and maintain machining accuracy, safeguarding the investment in PCD reaming tools.
-Misalignment and Dimensional Inaccuracies
- Avoiding Misalignment
Precision setup and alignment are fundamental to avoid misalignment, which can lead to significant dimensional inaccuracies. Inadequate use of PCD reamer tools can cause the cutting edges to not align perfectly, impacting the hole’s integrity.
- Ensuring Dimensional Accuracy
Employing the right strategies and equipment can greatly enhance the dimensional accuracy of reamed holes.
-Surface Finish Concerns
- Achieving Superior Surface Finishes
Optimizing reaming parameters is key to achieving the desired surface finish, a critical aspect of manufacturing aesthetics and functionality. Incorrect reamer size, cutting speed, or coolant selection can adversely affect the surface quality.
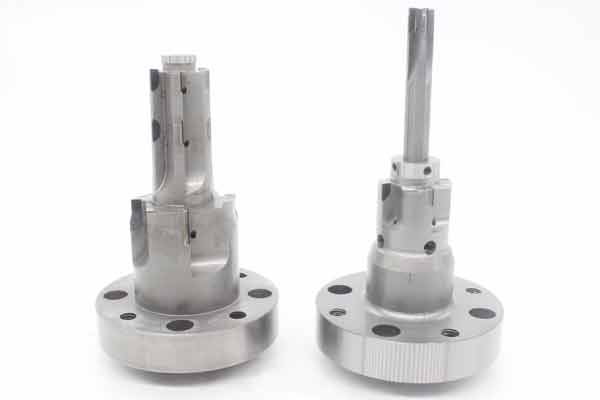
Advanced Techniques for PCD Reaming
Exploring advanced reaming techniques and tool designs can significantly improve efficienc anyd outcomes in PCD reaming processes, addressing issues like tool deformation and excessive primary clearance angle.
Real-World Applications of PCD Reamers
PCD reamers tools are instrumental in industries where precision is paramount, such as aerospace and automotive, where they contribute to the manufacturing of critical components.
Conclusion: Maximizing Efficiency with PCD Reamers
In conclusion, mastering the use of reamer tool is a journey of understanding both the tools and the materials they interact with. By addressing the common problems outlined in this guide, manufacturers can significantly enhance their machining processes, achieving higher accuracy, better finishes, and ultimately, superior products. This includes recognizing and addressing the frequent challenges associated with hole diameter variations and surface roughness during the reaming process with PCD reamers.