Pinnacle of Precision: Unleashing CNC Drilling Power
CNC drilling has revolutionized the world of machining, enabling precise hole creation with unparalleled accuracy. Achieving impeccable hole precision is not just a technical feat—it’s an art that requires a deep understanding of the process, meticulous planning, and the right techniques. In this article, we will explore the journey of elevating hole precision in CNC drilling, uncovering the strategies and insights that lead to flawless results.
Understanding the Significance of Precision
Precision is the bedrock of CNC drilling. Whether it’s in aerospace, automotive, or electronics, the quality of the end product hinges on the accuracy and consistency of the drilled holes. The ability to create holes with exact dimensions and perfect placement is what sets CNC drilling apart from traditional methods. Each drilled hole is a testament to the mastery of precision.
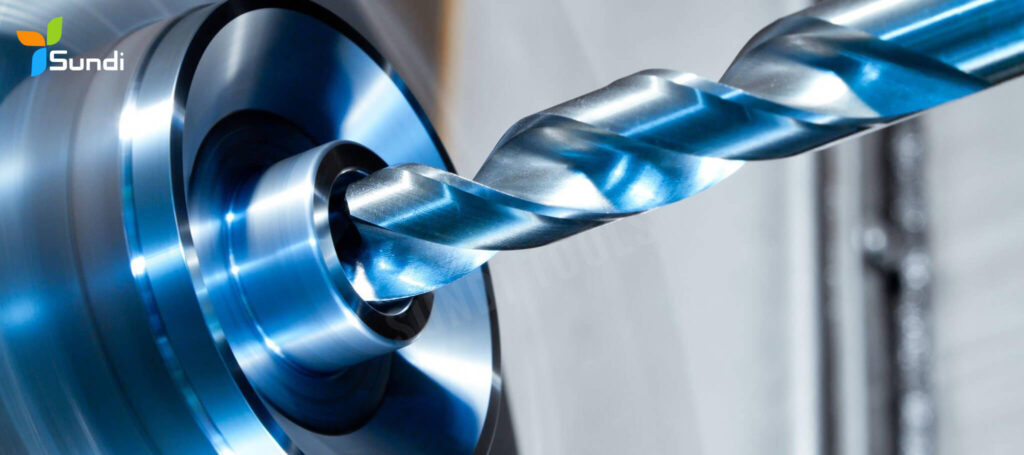
Factors that Influence Hole Precision
Several factors play a crucial role in achieving elevated hole precision:
- Tool Selection
Selecting the right drilling tool is paramount. Factors such as tool geometry, material, and coatings all impact the precision of the drilled hole. Specialized tools are designed to maintain accuracy throughout the drilling process.
- Cutting Parameters
Balancing spindle speed, feed rate, and depth of cut is essential for maintaining precision. These parameters are interrelated and must be optimized to prevent tool deflection and ensure consistent hole quality.
- Material Properties
Different materials react differently to drilling. Understanding the material’s hardness, composition, and heat conductivity helps in tailoring drilling parameters for optimal precision.
- Chip Management
Effective chip breaking and removal prevent tool clogging and heat buildup. Proper chip evacuation enhances precision by reducing the chances of tool breakage and material deformation.
- Coolant Application
Coolants play a dual role—reducing friction and dissipating heat. Proper coolant application ensures a clean cutting zone, preventing thermal damage and maintaining accuracy.
Advanced Techniques for Precision Enhancement
To elevate hole precision, advanced techniques come into play:
- Automated Tool Measurement
CNC machines equipped with automated tool measurement systems monitor tool wear and adjust drilling parameters in real-time, ensuring precision throughout the operation.
- High-Resolution Positioning
High-resolution positioning systems enable minute control over tool movement, translating to enhanced precision and accuracy.
- Tool Compensation
CNC systems can automatically compensate for tool wear, adjusting drilling paths to maintain accuracy even as the tool degrades.
The Role of Planning
Precision begins with meticulous planning:
- CAD/CAM Software
Advanced CAD/CAM software aids in designing precise drilling paths, simulating operations, and optimizing tool paths for accuracy.
- Defining Tolerances
Clearly defining tolerances for hole dimensions and positions ensures that the final product meets the required specifications.
- Pilot Holes and Test Runs
Using pilot holes as guides and conducting test runs on scrap materials help fine-tune drilling parameters and verify precision before actual drilling.
Elevating hole precision in CNC drilling is a journey that combines science, technology, and expertise. By understanding the factors that influence precision, adopting advanced techniques, and meticulous planning, machinists can achieve exceptional results. Each precisely drilled hole contributes to the overall quality of the final product, reflecting the dedication and mastery required for CNC drilling excellence.